Digital Twin technology is transforming the scene in the beating core of the manufacturing and automotive sectors. Consider a parallel universe in which every detail of a physical product or process is scrupulously copied and monitored digitally. Enter the Digital Twin, a technical marvel that replicates real-world entities in virtual space, delivering a dynamic and real-time equivalent. We uncover the significant influence of Digital Twins on manufacturing and autos as we dive into their rich tapestry.
This technology has become an essential component of a new age, from optimizing industrial processes to improving predictive maintenance in cars. This study will look into the symbiotic link between the physical and digital, revealing how digital twins enhance design, boost operational efficiency, and expand innovation frontiers. This blog takes you on a trip into the area where the virtual and physical collide, resulting in a revolutionary force that propels creativity, efficiency, and accuracy to unimaginable heights.
What is a Digital Twins? What is the purpose of the technology?
A Digital Twins is, at its heart, a virtual counterpart of a real thing, such as a product, process, or system. This replica is a dynamic, real-time counterpart that mimics the behavior, attributes, and situations of its actual counterpart. This coordinated interaction between the physical and digital domains allows organizations to acquire deeper insights, optimize performance, and make educated decisions throughout a product’s or process’s lifespan.
The Lights Of Digital Twin On The Manufacturing Industry To Move Forward Into The Future
Design and Prototyping
Digital Twin begins its journey in production at the design stage. Engineers and designers develop a virtual depiction of a product that includes minute features and standards. This digital prototype enables extensive simulations, allowing for the discovery and correction of problems before actual production begins. The end result is a finely calibrated masterpiece born of the confluence of computer precision and human imagination.
Predictive Maintenance
One of the transformational characteristics of the Digital Twin in manufacturing is its capacity to reinvent maintenance methods. Digital Twin provides predictive maintenance models by continually monitoring the performance of physical assets in real-time. These models use data analytics and machine learning to predict possible difficulties, allowing organizations to solve them proactively, save downtime, and extend their lifespan.
Smart Factories and IoT Integration
As production progresses towards Industry 4.0, the combination of the digital twin with the Internet of Things (IoT) gives rise to smart factories. Every piece of equipment, component, and process is transformed into a node in a digital network, resulting in a dynamic ecosystem in which data flows effortlessly between the physical and digital realms. This interconnection enables real-time monitoring, predictive maintenance, and process optimization, ushering in an era of unsurpassed efficiency.
Supply Chain Optimization
The Digital Twin’s influence extends beyond the manufacturing floor and throughout the supply chain. Manufacturers may digitally replicate their whole supply chain, from raw material sources to distribution networks. This comprehensive perspective improves demand forecasting, inventory management, and logistics optimization. Businesses may discover bottlenecks, improve cooperation, and respond quickly to changing market needs by viewing the whole supply chain in a digital space.
Alternate World Of Automobile Industry: Digital Twins
Design and Performance Optimization
Digital twins are critical to vehicle design and optimization in the automobile industry. Automobile manufacturers build virtual simulations of their cars, taking into account elements such as aerodynamics, fuel efficiency, and safety. This virtual testing environment enables quick iterations and fine-tuning prior to the production of actual prototypes. The end result is automobiles that are not only aesthetically beautiful but also precisely constructed for optimal performance and safety.
Connected Vehicles and Autonomous Driving
The capabilities of Digital Twin are propelling the development of linked automobiles and autonomous driving. The digital twin in a connected automotive ecosystem symbolizes the vehicle in the digital world, constantly exchanging data with the physical vehicle and its surroundings. This connectivity improves real-time monitoring, diagnostics, and upgrades over the air. For self-driving cars, Digital Twin acts as the virtual brain, simulating and improving driving algorithms in a variety of circumstances to ensure safe and efficient navigation.
Personalized Customer Experiences
The Digital Twin has an impact on the consumer experience by providing tailored and immersive interactions. Automakers may give consumers information regarding maintenance needs, performance indicators, and even customization choices by developing a virtual image of a car that reflects its real-time state. This degree of customization builds a greater bond between clients and their automobiles, ushering in a new ownership paradigm.
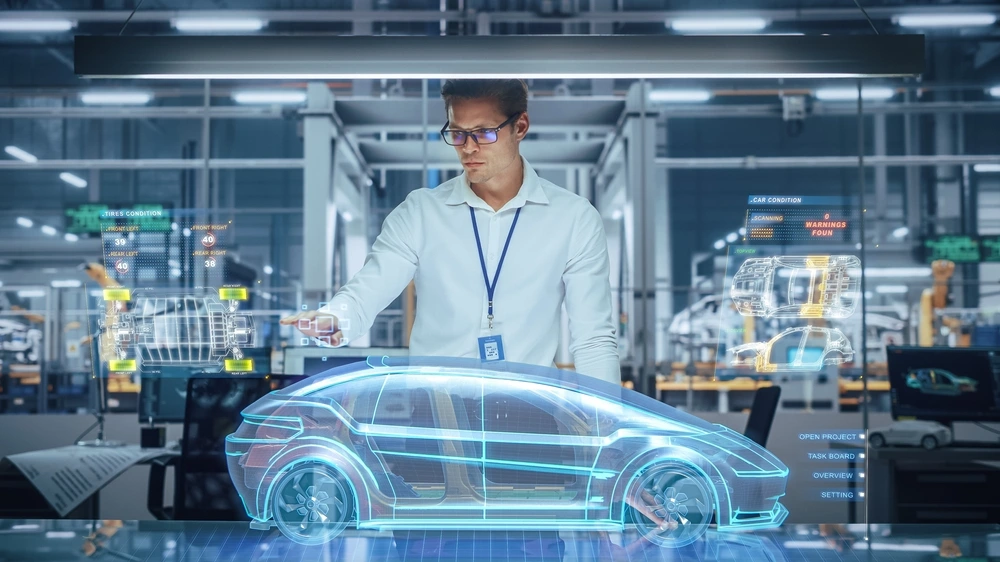
Lifecycle Management and Sustainability
The Digital Twin offers complete vehicle lifetime management, from design to end-of-life concerns. Manufacturers may monitor the performance and condition of cars in use, allowing for targeted recalls or upgrades. Furthermore, Digital Twin supports the optimization of recycling and disposal procedures, adding to the automobile industry’s environmental objectives.
The Future Is Beyond Boundaries
Integration with Emerging Technologies
Digital Twin’s path is far from monotonous. It is inextricably linked to new technologies such as artificial intelligence, augmented reality, and blockchain. AI improves Digital Twin’s predictive powers, AR enables immersive visualization, and blockchain assures safe and transparent data exchanges. This confluence expands the Digital Twin’s disruptive potential across industries.
Healthcare, Aerospace, and Beyond
While manufacturing and autos were early adopters, the Digital Twin’s effect extends to a wide range of industries. It assists in the creation of virtual models of organs for individualized medication in healthcare. It optimizes aircraft design and maintenance in the aerospace industry. As Digital Twin technology advances, so will its applications, altering how we approach complex systems and processes.